BLR
ist neu hier...
Guten Tag liebe Community,
ich mache dann mal in diesem Thread gleich die Vorstellung mit: Ich bin Steffen, komme aus Paderborn und fahre eine RSV4 APRC '12 in weiß.
Wenn ihr euch schon immer mal gefragt habt, was eigentlich bei der sogenannten Ventilspielkontrolle (20tkm/40tkm) gemacht wird oder ihr euch sogar selbst an's Schrauben machen wollt, dann seid ihr hier genau richtig.
Ich habe vor kurzem erst die Ventilspielkontrolle und -einstellung an meiner RSV4 vorgenommen. Im Internet gibt es leider kaum Threads auf Deutsch, in der das Verfahren gut erklärt ist.
In amerikanischen Foren wird viel über das Thema diskutiert und auch viele Tipps gegeben. Ich versuche alles hier unterzubekommen.
Die Ventilspielkontrolle sollte bei den APRC und nicht APRC sowie Factory-Modellen gleich sein. Wie es bei den Baujahren ab '17 aussieht, weiß ich leider nicht.
Okay, let´s go:
Zuerst eine Teileliste, was ihr alles genötigt:
Dichtungen und Ersatzteile:
2x 13,00€ Ventildeckeldichtung (vorderer, hinterer Zylinder Teilenummer 897443)
4x 4,90€ Dichtung Zündkerzenbohrung groß (Teilenummer 857074)
6x 3,40€ Dichtung Schrauben Ventildeckel (Teilenummer 898410)
1x Motordichtpaste eurer Wahl
Dichtungen und Ersatzteile falls eingestellt werden muss:
1x 47,90€ Kupplungsdeckeldichtung (Teilenummer 857451)
4x 1,40€ Dichtung Zündkerzenbohrung (Teilenummer 857043)
8x 1,20€ Unterlegscheibe aus Kupfer für Nockenwellenlagerdeckel (Teilenummer 857042)
1x Loctite 243 Mittelfest
1x Motoröl und Ölfilter, falls ihr das verwendete Motoröl/Filter nicht wieder benutzen wollt
4x ~40€ Zündkerzen NGK-R CR10E (braucht ihr nicht unbedingt, aber wenn ihr schon einmal soweit seid)
Werkzeugliste:
- alles mögliche an Nüssen und Inbusschlüssel/Aufsätze
- Fühlerlehren zum Messen des Ventilspiels (ich habe welche mit 0.01mm Abständen bis 0.1mm, so kann man genau messen)
- Drehmomentschlüssel bis 15 NM (z.B. Proxxon 23345 MicroClick-Drehmomentschlüssel MC15 3–15Nm)
- 17er Zündkerzenschlüssel
was ihr an Werkzeug benötigt, falls eingestellt werden muss:
- elektronischer Messschieber zum Messen der Shims (muss nicht sein, ein normaler reicht auch, macht das Leben aber einfacher)
- Spezialwerkzeug 020852Y (ihr könnt hier auch eine Gewindestange nehmen)
- Spezialwerkzeug 020851Y (ihr könnt hier auch einen gebogenen Inbusschlüssel nehmen)
- Spezialwerkzeug 020914Y (falls ihr das Kokusan Schwungrad habt)
- Spezialwerkzeug 020913Y (falls ihr das Kokusan Schwungrad habt)
- Spezialwerkzeug 020850Y (wird meiner Meinung nach nicht benötigt da sich in der Stellung für den Ausbau der Nockenwellen nichts verdrehen kann, wenn man vorsichtig arbeitet und Kurbelwelle arritiert ist. Falls ihr das Werkzeug dennoch verwenden wollt, dann müsst ihr Kupplungskorb usw. ebenfalls ausbauen (macht das nicht!))
- Spezialwerkzeug 020865Y (wird definitiv benötigt)
- Magnet für Tassenstößel
- Drehmomentschlüssel mit 30 NM (z.B. STIER Drehmomentschlüssel mit Umschaltknarre 1/2'' Aufnahme 10-50 Nm)
Okay, soweit zu den Vorbereitungen. Fangen wir also an.
Das wichtigste zuerst:
Nehmt euch das Werkstatthandbuch zur Hand. Diese Anleitung soll nur den Ablauf verdeutlichen und ersetzt keinesfalls das Werkstatthandbuch!
Weg freiräumen
Baut die Seitenverkleidungen, den Sitz und den Tank ab.
Danach entfernt ihr die ECU auf dem Luftfilterkasten. Schiebt dazu einfach die Entriegelung der Steckverbindungen zur Seite, die Stecker sollten sich nun von allein lösen.
Löst nun die Schrauben für die Düsen auf dem Luftfilterkasten und zieht alle vier heraus, löst die Befestigungsschraube des Kabelbaums am Luftfilterkasten und zieht die ganzen Kabel zur Seite.
Löst nun die Schrauben für den Luftfilterkasten und nehmt den Deckel ab.
In dem Luftfilterkasten sind vier Ansaugtrichter, löst die Schrauben und nehmt die Ansaugtrichter heraus.
Ihr könnt nun den unteren Luftfilterkasten herausnehmen, löst von ihm alle an ihm befindlichen gesteckten Kabel. Auch die beiden Schläuche links und rechts müsst ihr abziehen.
Zur Sicherheit habe ich in die Drosselklappenöffunungen der Zylinder Küchenrollenpapier gesteckt, sodass kein Staub oder Schmutz hineinfallen kann.
Das ganze sollte nun so aussehen:
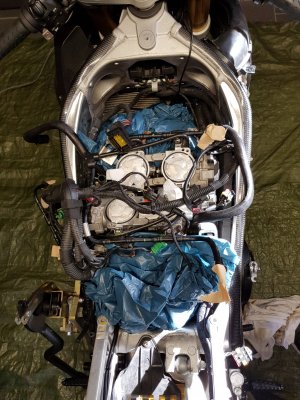
(Ich habe hier die Ventildeckel bereits ab gehabt und mit Folie zugedeckt, sodass keine Teile oder Staub in den Motorraum gelangen können)
Nun müsst ihr die Schläuche lösen, die sich über den Ventildeckel ziehen. Für die Zylinderbank am Kühler müsst ihr von der linken Seite den Lüfter abmontieren, sodass ihr mit einer Zange an die Sicherung des Schlauches kommt um ihn abziehen zu können.
An der Zylinderbank am Heck kommt ihr ohne weitere Demontage von Teilen an die Schlauchschelle heran.
Nun löst die Zündspulen und holt mit einem Zündkerzenschlüssel die Zündkerzen heraus. Steckt in das Loch wieder Küchenpapier, sodass keine Teile in den Motorbrennraum fallen können.
Ihr könnt nun die Schrauben der Ventildeckel (3 Stück pro Deckel) lösen und die Ventildeckel abnehmen. Ihr seht nun die Ein- und Auslassnockenwellen der vorderen und hinteren Zylinderbank.
Schraubt nun an der Kupplungsseite den silbernen Deckel ab.
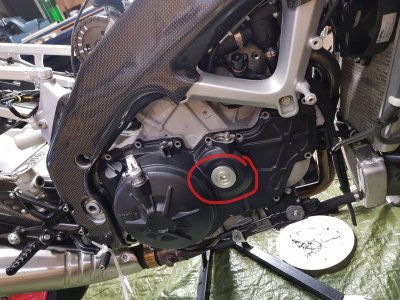
Keine Sorge, das Öl befindet sich weiter unten und es wird nichts herausfließen. Wenn ihr nun durch die Öffnung schaut, seht ihr ein Zahnrad mit einer Aufnahme für einen Inbusschlüssel. Steck z.B. eine Ratsche mit Aufnahme hinein, damit ihr die Kurbelwelle und somit auch die Nockenwellen drehen könnt.
Der Motor wird in Fahrtrichtung gedreht!
Ventilspiel messen
Fangt z.B. bei der hinteren Zylinderbank an. Dreht die Kurbelwelle jeweils so, dass ihr zwischen Nockenwelle und Tassenstößel messen könnt:
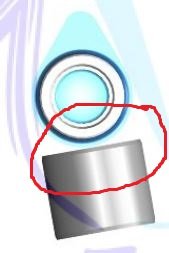
Nehmt euch also die Fühlerlehren zur Hand und fangt für die Einlassnockenwelle mit 0.10mm an. Passt die Fühlerlehre nicht zwischen Nocke und Tassenstößel, so muss das Ventilspiel eingestellt werden.
Die jeweils zum motorinneren liegende Nockenwelle ist die Einlassnockenwelle. Hier muss das Spiel zwischen 0.10mm und 0.15mm liegen. Notiert euch die gemessenen Werte für jedes Ventil/Nocke.
Auf der Auslassseite solltet ihr Werte zwischen 0.20mm und 0.25mm messen. Falls dem nicht so ist, muss das Ventilspiel eingestellt werden.
Falls alle Werte in Ordnung und in der Toleranz liegen, könnt ihr beruhigt sein und alles wieder zusammenbauen.
Toleranz Einlassnockenwelle: 0.10 – 0.15 mm
Toleranz Auslassnockenwelle: 0.20 – 0.25 mm
ich mache dann mal in diesem Thread gleich die Vorstellung mit: Ich bin Steffen, komme aus Paderborn und fahre eine RSV4 APRC '12 in weiß.
Wenn ihr euch schon immer mal gefragt habt, was eigentlich bei der sogenannten Ventilspielkontrolle (20tkm/40tkm) gemacht wird oder ihr euch sogar selbst an's Schrauben machen wollt, dann seid ihr hier genau richtig.
Ich habe vor kurzem erst die Ventilspielkontrolle und -einstellung an meiner RSV4 vorgenommen. Im Internet gibt es leider kaum Threads auf Deutsch, in der das Verfahren gut erklärt ist.
In amerikanischen Foren wird viel über das Thema diskutiert und auch viele Tipps gegeben. Ich versuche alles hier unterzubekommen.
Die Ventilspielkontrolle sollte bei den APRC und nicht APRC sowie Factory-Modellen gleich sein. Wie es bei den Baujahren ab '17 aussieht, weiß ich leider nicht.
Okay, let´s go:
Zuerst eine Teileliste, was ihr alles genötigt:
Dichtungen und Ersatzteile:
2x 13,00€ Ventildeckeldichtung (vorderer, hinterer Zylinder Teilenummer 897443)
4x 4,90€ Dichtung Zündkerzenbohrung groß (Teilenummer 857074)
6x 3,40€ Dichtung Schrauben Ventildeckel (Teilenummer 898410)
1x Motordichtpaste eurer Wahl
Dichtungen und Ersatzteile falls eingestellt werden muss:
1x 47,90€ Kupplungsdeckeldichtung (Teilenummer 857451)
4x 1,40€ Dichtung Zündkerzenbohrung (Teilenummer 857043)
8x 1,20€ Unterlegscheibe aus Kupfer für Nockenwellenlagerdeckel (Teilenummer 857042)
1x Loctite 243 Mittelfest
1x Motoröl und Ölfilter, falls ihr das verwendete Motoröl/Filter nicht wieder benutzen wollt
4x ~40€ Zündkerzen NGK-R CR10E (braucht ihr nicht unbedingt, aber wenn ihr schon einmal soweit seid)
Werkzeugliste:
- alles mögliche an Nüssen und Inbusschlüssel/Aufsätze
- Fühlerlehren zum Messen des Ventilspiels (ich habe welche mit 0.01mm Abständen bis 0.1mm, so kann man genau messen)
- Drehmomentschlüssel bis 15 NM (z.B. Proxxon 23345 MicroClick-Drehmomentschlüssel MC15 3–15Nm)
- 17er Zündkerzenschlüssel
was ihr an Werkzeug benötigt, falls eingestellt werden muss:
- elektronischer Messschieber zum Messen der Shims (muss nicht sein, ein normaler reicht auch, macht das Leben aber einfacher)
- Spezialwerkzeug 020852Y (ihr könnt hier auch eine Gewindestange nehmen)
- Spezialwerkzeug 020851Y (ihr könnt hier auch einen gebogenen Inbusschlüssel nehmen)
- Spezialwerkzeug 020914Y (falls ihr das Kokusan Schwungrad habt)
- Spezialwerkzeug 020913Y (falls ihr das Kokusan Schwungrad habt)
- Spezialwerkzeug 020850Y (wird meiner Meinung nach nicht benötigt da sich in der Stellung für den Ausbau der Nockenwellen nichts verdrehen kann, wenn man vorsichtig arbeitet und Kurbelwelle arritiert ist. Falls ihr das Werkzeug dennoch verwenden wollt, dann müsst ihr Kupplungskorb usw. ebenfalls ausbauen (macht das nicht!))
- Spezialwerkzeug 020865Y (wird definitiv benötigt)
- Magnet für Tassenstößel
- Drehmomentschlüssel mit 30 NM (z.B. STIER Drehmomentschlüssel mit Umschaltknarre 1/2'' Aufnahme 10-50 Nm)
Okay, soweit zu den Vorbereitungen. Fangen wir also an.
Das wichtigste zuerst:
Nehmt euch das Werkstatthandbuch zur Hand. Diese Anleitung soll nur den Ablauf verdeutlichen und ersetzt keinesfalls das Werkstatthandbuch!
Weg freiräumen
Baut die Seitenverkleidungen, den Sitz und den Tank ab.
Danach entfernt ihr die ECU auf dem Luftfilterkasten. Schiebt dazu einfach die Entriegelung der Steckverbindungen zur Seite, die Stecker sollten sich nun von allein lösen.
Löst nun die Schrauben für die Düsen auf dem Luftfilterkasten und zieht alle vier heraus, löst die Befestigungsschraube des Kabelbaums am Luftfilterkasten und zieht die ganzen Kabel zur Seite.
Löst nun die Schrauben für den Luftfilterkasten und nehmt den Deckel ab.
In dem Luftfilterkasten sind vier Ansaugtrichter, löst die Schrauben und nehmt die Ansaugtrichter heraus.
Ihr könnt nun den unteren Luftfilterkasten herausnehmen, löst von ihm alle an ihm befindlichen gesteckten Kabel. Auch die beiden Schläuche links und rechts müsst ihr abziehen.
Zur Sicherheit habe ich in die Drosselklappenöffunungen der Zylinder Küchenrollenpapier gesteckt, sodass kein Staub oder Schmutz hineinfallen kann.
Das ganze sollte nun so aussehen:
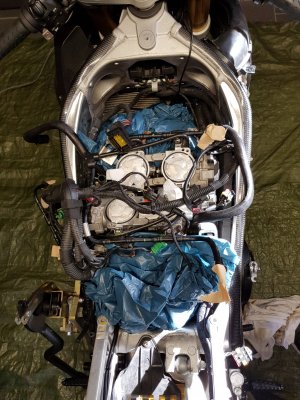
(Ich habe hier die Ventildeckel bereits ab gehabt und mit Folie zugedeckt, sodass keine Teile oder Staub in den Motorraum gelangen können)
Nun müsst ihr die Schläuche lösen, die sich über den Ventildeckel ziehen. Für die Zylinderbank am Kühler müsst ihr von der linken Seite den Lüfter abmontieren, sodass ihr mit einer Zange an die Sicherung des Schlauches kommt um ihn abziehen zu können.
An der Zylinderbank am Heck kommt ihr ohne weitere Demontage von Teilen an die Schlauchschelle heran.
Nun löst die Zündspulen und holt mit einem Zündkerzenschlüssel die Zündkerzen heraus. Steckt in das Loch wieder Küchenpapier, sodass keine Teile in den Motorbrennraum fallen können.
Ihr könnt nun die Schrauben der Ventildeckel (3 Stück pro Deckel) lösen und die Ventildeckel abnehmen. Ihr seht nun die Ein- und Auslassnockenwellen der vorderen und hinteren Zylinderbank.
Schraubt nun an der Kupplungsseite den silbernen Deckel ab.
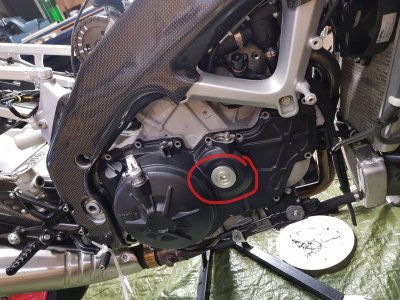
Keine Sorge, das Öl befindet sich weiter unten und es wird nichts herausfließen. Wenn ihr nun durch die Öffnung schaut, seht ihr ein Zahnrad mit einer Aufnahme für einen Inbusschlüssel. Steck z.B. eine Ratsche mit Aufnahme hinein, damit ihr die Kurbelwelle und somit auch die Nockenwellen drehen könnt.
Der Motor wird in Fahrtrichtung gedreht!
Ventilspiel messen
Fangt z.B. bei der hinteren Zylinderbank an. Dreht die Kurbelwelle jeweils so, dass ihr zwischen Nockenwelle und Tassenstößel messen könnt:
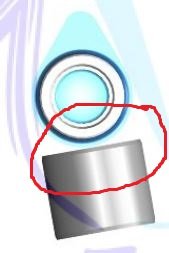
Nehmt euch also die Fühlerlehren zur Hand und fangt für die Einlassnockenwelle mit 0.10mm an. Passt die Fühlerlehre nicht zwischen Nocke und Tassenstößel, so muss das Ventilspiel eingestellt werden.
Die jeweils zum motorinneren liegende Nockenwelle ist die Einlassnockenwelle. Hier muss das Spiel zwischen 0.10mm und 0.15mm liegen. Notiert euch die gemessenen Werte für jedes Ventil/Nocke.
Auf der Auslassseite solltet ihr Werte zwischen 0.20mm und 0.25mm messen. Falls dem nicht so ist, muss das Ventilspiel eingestellt werden.
Falls alle Werte in Ordnung und in der Toleranz liegen, könnt ihr beruhigt sein und alles wieder zusammenbauen.
Toleranz Einlassnockenwelle: 0.10 – 0.15 mm
Toleranz Auslassnockenwelle: 0.20 – 0.25 mm
Zuletzt bearbeitet: